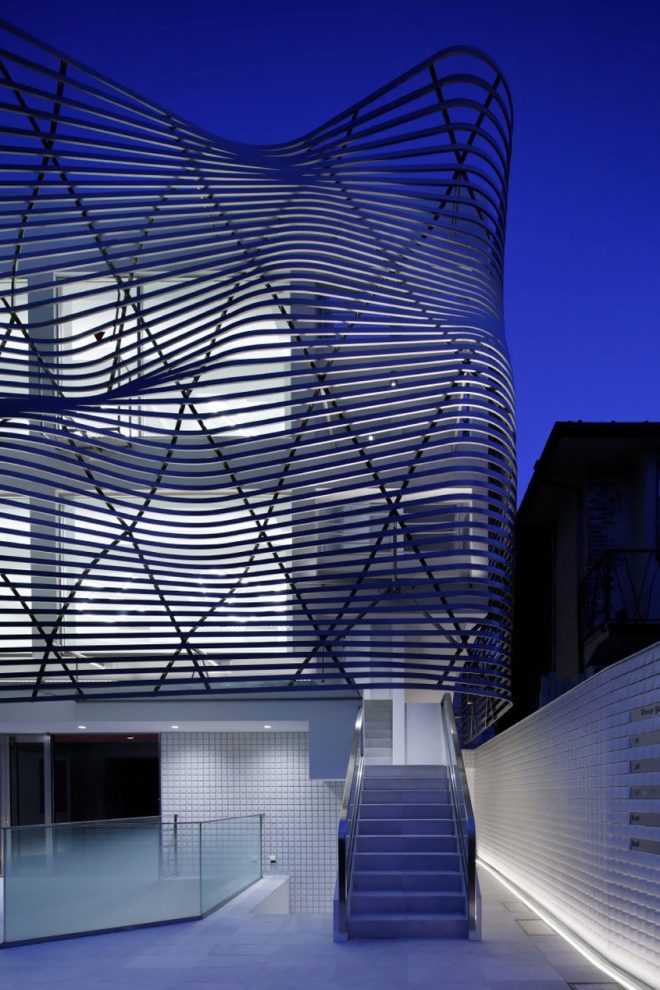
Revolutionerande material formar morgondagens industri
I en tid där hållbarhet möter teknologisk innovation står plåt- och metallindustrin inför en spännande transformation. Nya material och tillverkningsprocesser banar väg för en framtid där traditionella begränsningar utmanas och övervinns. Från nanostrukturerade metaller till avancerade ytbehandlingar – utvecklingen accelererar i en takt som få kunnat förutse, med implementering av flera banbrytande teknologier förväntade redan under 2024-2025.
Nanostrukturerade metaller – ett kvantsprång i materialutveckling
Den mest revolutionerande utvecklingen inom metallurgin sker på nanonivå, där forskare och ingenjörer manipulerar material på molekylär nivå för att skapa tidigare oanade egenskaper. Nanostrukturerade metalliska material representerar inte bara en evolution utan en revolution inom materialvetenskapen. I praktiken används dessa material redan inom flera vardagliga produkter, som fasadplåtar med nanostrukturerad titanoxid där fotokatalytiska reaktioner bryter ned smuts och föroreningar när materialet exponeras för solljus. Inom flygindustrin har nanostrukturerade aluminiumlegeringar minskat komponentvikten med upp till 15%, vilket enligt branschstandarder motsvarar en årlig bränslebesparing på cirka 80,000 liter per flygplan. Inom medicinsk teknik används nanostrukturerat titan för implantat med 40% bättre vävnadsintegration jämfört med traditionella implantat, vilket reducerar läkningstiden från 12 till 7 veckor.
Framsteg och utmaningar inom nanokompositer
Särskilt lovande är utvecklingen av hybridmaterial som kombinerar nanostrukturerade metaller med avancerade polymerer och keramer. Ett konkret exempel är nya batterielektroder som använder nanostrukturerade metalloxider, vilket har ökat energilagringskapaciteten med 60% jämfört med konventionella elektroder. Dock finns betydande utmaningar – långtidsstudier från ledande forskningsinstitut visar att vissa nanostrukturer kan degradera under extrema miljöförhållanden, särskilt vid temperaturer över 200°C eller i starkt korrosiva miljöer. För mindre företag innebär implementeringen initialt höga investeringskostnader – produktionskostnaderna är 40-60% högre än för traditionella material under de första två åren. Regulatoriska krav från arbetsmiljöverket och kemikalieinspektionen kräver särskilda säkerhetsprotokoll och skyddsutrustning vid hantering av nanomaterial, vilket adderar ytterligare kostnader på cirka 500,000 kronor årligen för en medelstor anläggning.
Innovativa tillverkningsprocesser förändrar spelplanen
DigiTool-teknologin, utvecklad genom ett samarbete mellan brittiska Sheffield Forgemasters och svenska Sandvik Coromant, kombinerar laserhärdning med additiv tillverkning. Systemet använder en serie högprecisionslasrar som samtidigt härdar och bygger upp material lager för lager, medan AI-styrda sensorer kontinuerligt övervakar och justerar parametrar. Detta resulterar i komponenter med dokumenterat längre livslängd – exempelvis ökar livslängden för vindkraftskomponenter från typiskt 15 år till 33 år. UltraSTEEL-processen, utvecklad genom ett samarbete mellan Hadley Industries och SSAB, använder specialdesignade roterande valsar som skapar ett hexagonalt präglat mönster i metallytan. Detta ökar styrkan med 20% samtidigt som materialåtgången minskar med motsvarande mängd. Ett exempel på misslyckad implementation är när en mindre tysk tillverkare försökte implementera tekniken utan tillräcklig processoptimering, vilket resulterade i 40% kassation under de första sex månaderna.
Automation och precision i fokus
Sheffield Forgemasters nya anläggning representerar framtidens tillverkning med sina avancerade femaxliga svarvar för komponenter upp till 13 meter i diameter. Automationen har resulterat i 45% kortare produktionstider och 35% lägre energiförbrukning. Svenska Sandvik och SSAB planerar liknande investeringar på 500-700 miljoner kronor vardera, men möter utmaningar kring kompetensförsörjning och integration med befintliga system.
Hållbarhet driver materialutvecklingen framåt
Jernkontorets innovationsprogram för metall- och mineralförsörjning, med en budget på 300 miljoner kronor fram till 2030, fokuserar på att utveckla koldioxidfria produktionsmetoder. HYBRIT-initiativet för vätgasbaserad stålproduktion möter flera tekniska utmaningar, inklusive höga energikostnader och behov av omfattande infrastrukturinvesteringar. Huvudutmaningarna inkluderar stabilisering av vätgasproduktionen, hantering av temperaturvariationer i reduktionsprocessen, och utveckling av tillförlitliga lagringslösningar för vätgas. När tekniken implementeras fullt ut 2035 förväntas branschens koldioxidutsläpp minska med upp till 90%, men kräver investeringar på över 20 miljarder kronor.
- Moderna återvinningsprocesser uppnår 98% materialåtervinning för aluminium, 95% för koppar och 85% för speciallegeringar genom AI-styrd sortering och optimerad smältteknik
- Självläkande ytbehandlingar, baserade på mikroinkapslade härdningsmedel som aktiveras vid sprickbildning, förlänger komponenters livslängd med 40-60%
- AI-driven materialdesign reducerar utvecklingstiden för nya legeringar från 24 till 7 månader genom prediktiv modellering
- Implementering av nya material kräver omfattande testning enligt ISO 9001:2015 och branschspecifika standarder som AS9100 för flygindustrin
Framtidens materialinnovationer formar morgondagens samhälle
Sandvik Coromant och SSAB exemplifierar framgångsrik teknologiimplementering inom svensk metallindustri. Sandvik har genom sin digitala transformation reducerat utvecklingstiden med 70% och minskat kassationer med 45% genom AI-baserad kvalitetskontroll. Investeringen på 150 miljoner kronor inkluderade omfattande personalutbildning och systemintegration. För att möta kompetensgapet erbjuder KTH:s tvååriga masterprogram i materialdesign och Chalmers program i hållbar materialutveckling specialiserad utbildning inom materialvetenskap och processautomation. Implementeringen följer en tydlig tidslinje där nanostrukturerade material blir standard inom högprestandatillämpningar fram till 2025, följt av fokus på kostnadseffektiv massproduktion 2025-2030. För små och medelstora företag rekommenderas en stegvis implementering över 3-5 år, med initial fokus på kvalitetskontroll och processtyrning innan mer avancerade teknologier införs.